
The D-292 ACAP on its maiden flight late in August 1985, a year behind
schedule.

The all-composite Bell Design D-292 ACAP was based on the Model 222 design.
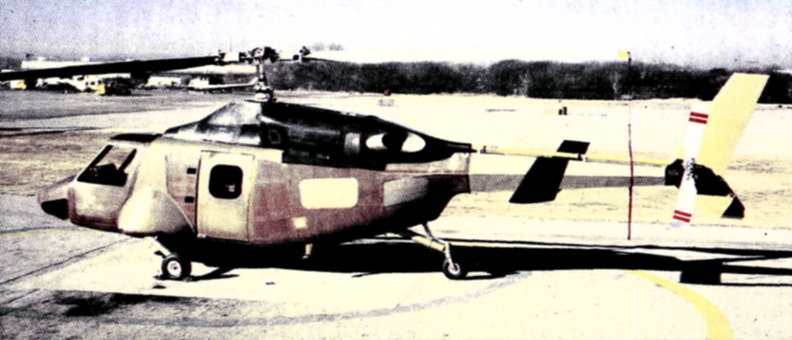
One of the ACAP prototypes seen before any painting or markings were applied.



A sequence showing a crash test performed with one of theACAP airframes.
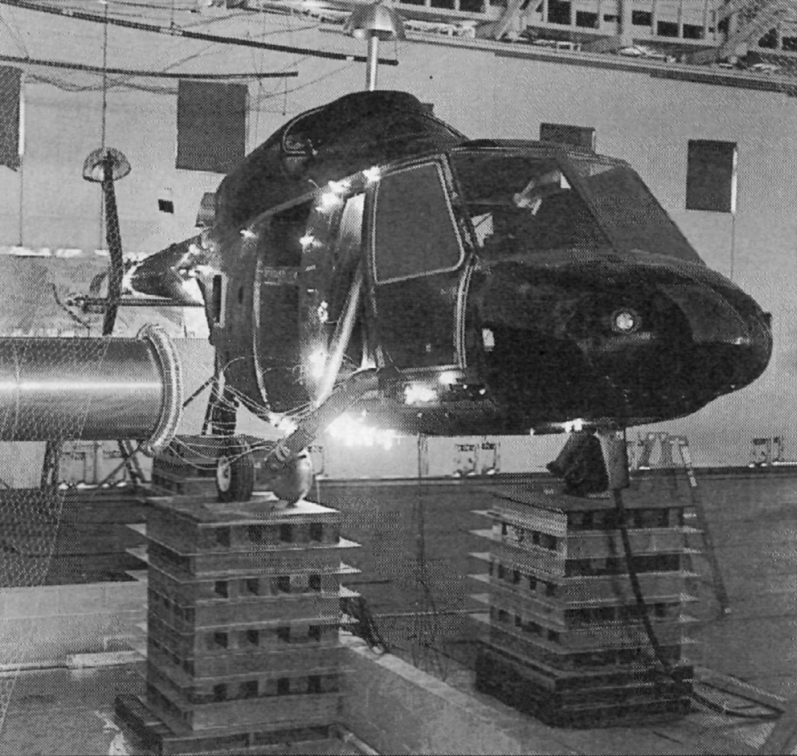
A Bell D-292 tested by Boeing to study atmospheric electricity
hazards. The sparking in the picture occurs
at structural joints, where the current arcs across the skin instead of flowing
through the
structure.
Arcing
also
occurs at joints in the aluminium wire mesh which covers the fuselage's composite
skin.
|
BELL HELICOPTER
D-292 ACAP
(Advanced Composite Airframe Program)
Info: all-composite research helicopter
Powerplant: 2 x Avco Lycoming 510kW LTS 101-750C-1
turboshafts
Significant date: 30 August 1985 (first flight)
Under the Army's Advanced Composite
Airframe Program (ACAP),
Bell Helicopter Textron was one of
the two manufacturers (the other
being Sikorsky) awarded a contract
to design and develop a prototype of
an all-composite helicopter. Phase I
of this programme, which consisted
of the engineering design and design
support testing, was completed by
the end of 1982. The construction
and testing of three airframes (Phase
II), began in October 1982. The first
airframe was a tool-proofing article
(TPA) used for repairability demonstrations
and ballistic testing, while
the second airframe became the
flight-test vehicle (FTV) and accomplished
its initial hover flight on 30
August 1985, over a year after the initially scheduled date. This was caused
by both a series of walkouts from Bell employees and a shortage of funds, which
led
Bell
to ask the Government for extra funding.
In addition to 15 hours of ground
running and 50 hours of flight
testing, which were completed in
October 1985, the D-292 was used
for shake testing and controls proof
loading. A five-phase militarisation
test and evaluation program
(MT&E) began in 1985 and was
completed in 1988, following evaluation
of undercarriage crashworthiness,
lightning protection system,
internal acoustics and additional repairability
demonstrations. This
program included dropping the
helicopter airframe from 42 ft in
September 1987 at the NASA
Langley Research Centre to demonstrate
the capability of meeting stringent
military crash survivability requirements.
This included a 50 ft/sec impact velocity at an aircraft
attitude of ten degrees roll and ten
degrees nose up pitch without any
apparent serious injuries to the four
dummy occupants (this impact
velocity was comparable to a free fall
from a three-storey building).
Another major advancement demonstrated
by the Bell ACAP design
during these tests was the fuel system which totally contained the fuel
during the drop test, thus reducing
the risk of post-crash fires. But the
main purpose of the ACAP programme
was to achieve the US
Army's goal of reducing weight and
cost, as well as improving military
helicopter characteristics, by demonstrating
the application of advanced
composite materials. In this
sphere, the Bell D-292 featured a
weight reduction of 22 per cent in
the airframe structure, a 17 per cent
saving in cost, survivability in a
vertical crash, and reduced radar
signature. These comparisons were
made possible because Bell and
Sikorsky each also designed a duplicate
aircraft of current conventional
metal construction.
Thus the ACAP programme
proved successful in meeting its
objectives to demonstrate the use of
advanced composites in a fully
militarized airframe. This fruitful
experience was to be used in the
development of the future LHX
light attack/armed reconnaissance
helicopter.
Much less known is the experiment that was conducted in 1986 by the
Boeing Military Airplane Company as part of an $8.3
million US Air Force study on atmospheric electricity
hazards. Using a Bell D-292 airframe provided by the US
Army's ACAP program,
the BMAC team investigated methods of protecting
electronic equipment in all-composite airframes from lightning
strikes. The lightning simulation was capable of producing
200,000A/1.6Mv. The study was completed in June of the following
year.
Population: 3 [the flying article received Army
serial 85-24371]
Specs:
Main rotor
diameter: 42 ft (12.80 m)
Length: 40 ft 5 in (12.32 m)
Height: 11 ft 2 in (3.40 m)
Maximum takeoff weight: 7,485 lb (3,395 kg)
Empty weight: 5,765 lb (2,615 kg)
Crew/passengers: 4 (2 crew, 2 passengers)


A
glance inside the D-292 ACAP helicopter's all-composite mainframe.
|